Products
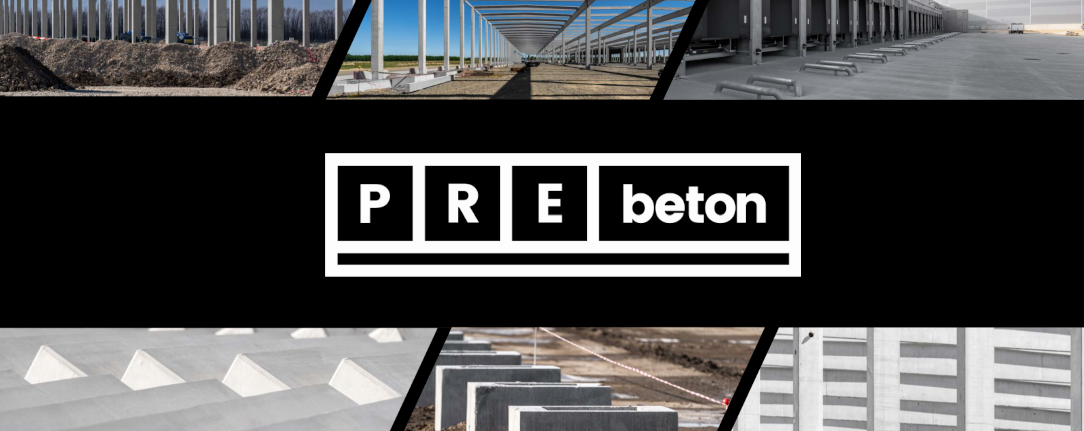
The company manufactures the prefabricated reinforced concrete elements on a 6-hectare factory site in Erdőtelek. Production takes place in two heated, winterized production halls with the most modern technologies. Based on the product plans, the elements are manufactured with the help of a unique template park and own concrete plant, in the case of individual products with wood and steel hybrid formwork, for the preparation of which our own joinery and locksmith factory is available.
Concrete block
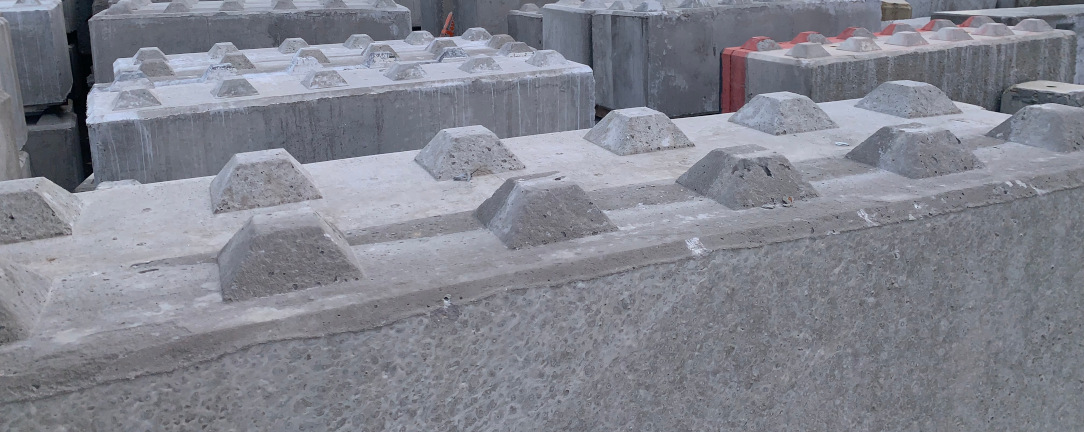
With our concrete blocks – also known as Lego bricks – we offer a flexible and cost-effective product for temporary buildings, warehouses, bulk material storage, partitioning and retaining walls.Thanks to the simple application, no mounting material is required.
Docking station
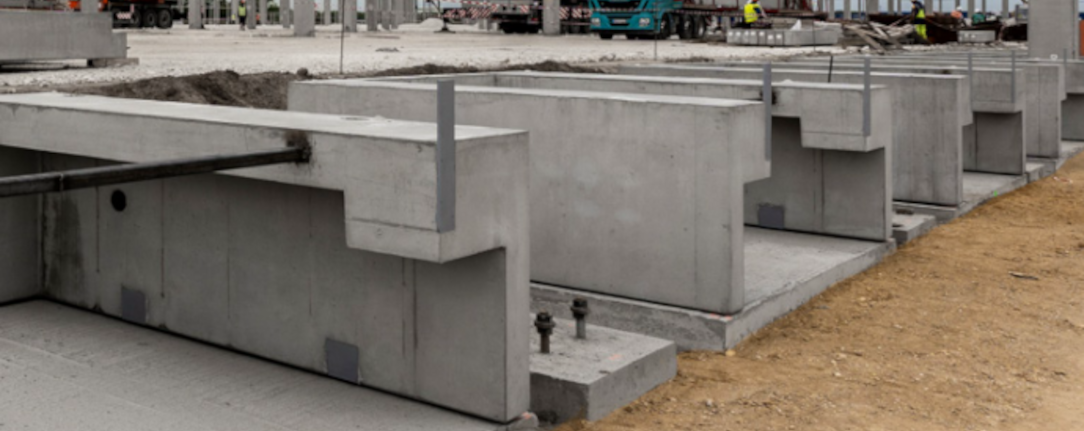
The truck docking shaft is an excellent structure for accessing warehouses, goods loaders and department stores by truck and forklift. The elements made by our company are manufactured and delivered in one piece, making installation easier, and if required, the elements can be manufactured separated on their axis of symmetry. Our docking stations are designed to accommodate several types of scissor lift or tilt ramps.
Balcony
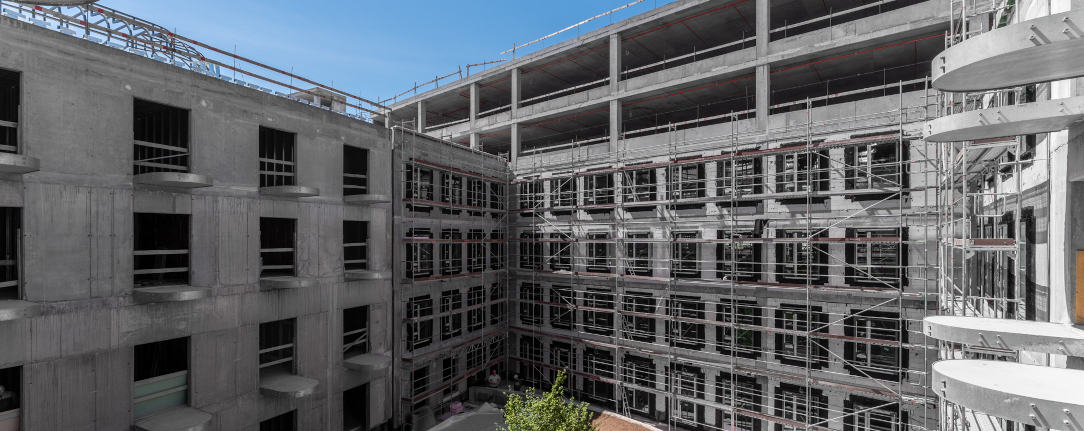
Prefabricated balcony slabs can be a rational and cost-effective solution in construction. Thanks to its design, it can be installed quickly and safely, so it can be used for new structures or renovation of existing buildings.
Wall panel
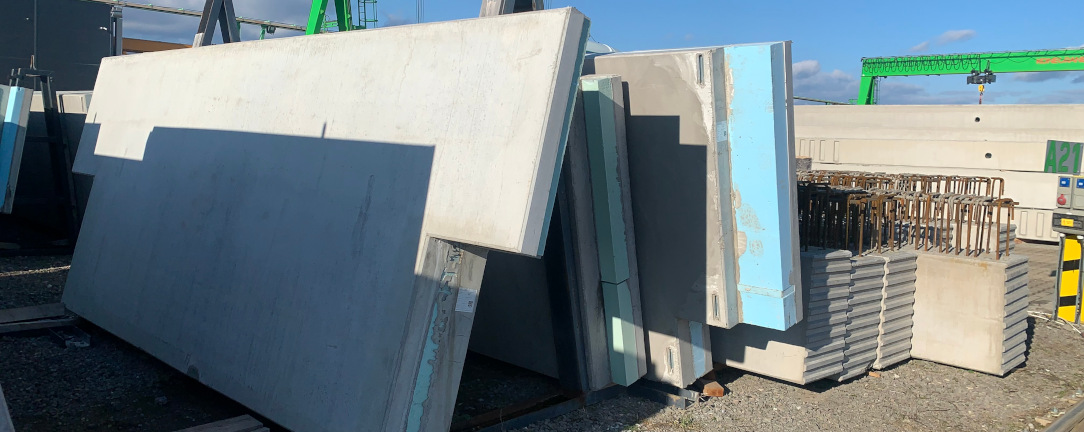
Prefabricated plinth can be made with one, two or three layers, open or closed cellular thermal insulation.
The single-layer structure is made with a design without thermal insulation.
In a two-layer structure, 1 layer of heat insulator is placed on the outside of the self-supporting panel.
In a three-layer structure, an intermediate heat-insulating plate is placed between the load-bearing inner bark and the external, visible bark.
The elements are attached to the pillars and foundation bodies by fittings placed during production.
The single-layer structure is made with a design without thermal insulation.
In a two-layer structure, 1 layer of heat insulator is placed on the outside of the self-supporting panel.
In a three-layer structure, an intermediate heat-insulating plate is placed between the load-bearing inner bark and the external, visible bark.
The elements are attached to the pillars and foundation bodies by fittings placed during production.
Beam
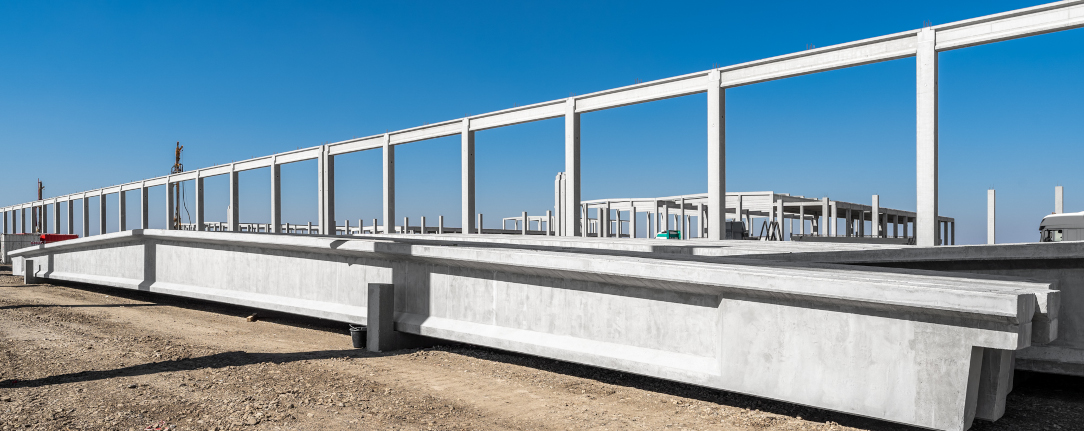
The main, horizontal, load-bearing elements of buildings are beams and main supports. In terms of shape, they can be rectangular or profiled. In beam production, cost-effectiveness is important. Based on the loads and spans, soft iron and prestressed beam production is possible, which is determined by the static designer. By installation, we can talk about roof supports, intermediate slab beams and footbeams.
Facade panel
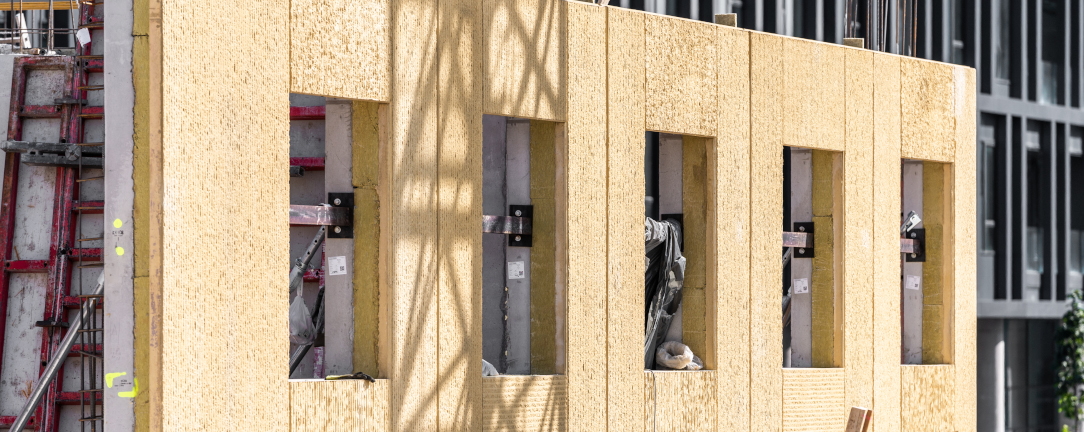
The façade largely determines the perception of the building,highlights itfrom the other structures and forms a lasting memory for the visitor. The concrete elements of the façade are composed of separate units, separate pieces into a single complex and homogeneous system, which follows the shape of thebuilding in the desired shape. The concrete elements sit on a strip-shaped base body or on concrete brackets formed on the basement wall, optionally on steel brackets fixed to the basement wall, and are loaded vertically on top of each other. The façade elements are fixed to the supporting structure of the building on each floor level with steel fittings against wind pressure, suction or overturning and they are aligned with each other. The solution is therefore favorable for the use of the building structure, as the self-weight of the elements appears on the basement level/ground floor.
Cup
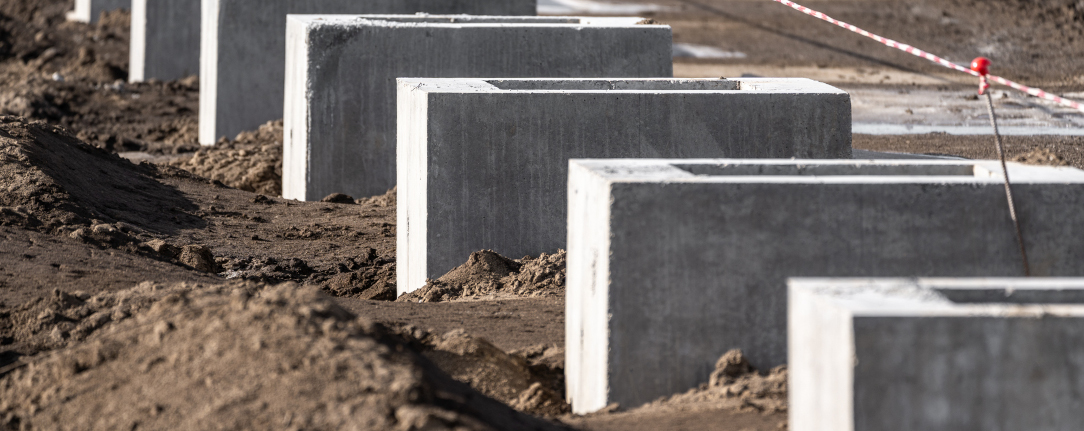
Nowadays, the impaction of the pillars of reinforced concrete frame structures is ensured by prefabricated cup necks. For the base bodies , the cup neck is prefabricated, the base block is a monolithic reinforced concrete structure (flat foundation) but can be used in combination with any deep foundation method. ( well foundation, basic block, micro or macro pile etc.)
Prestressed slab
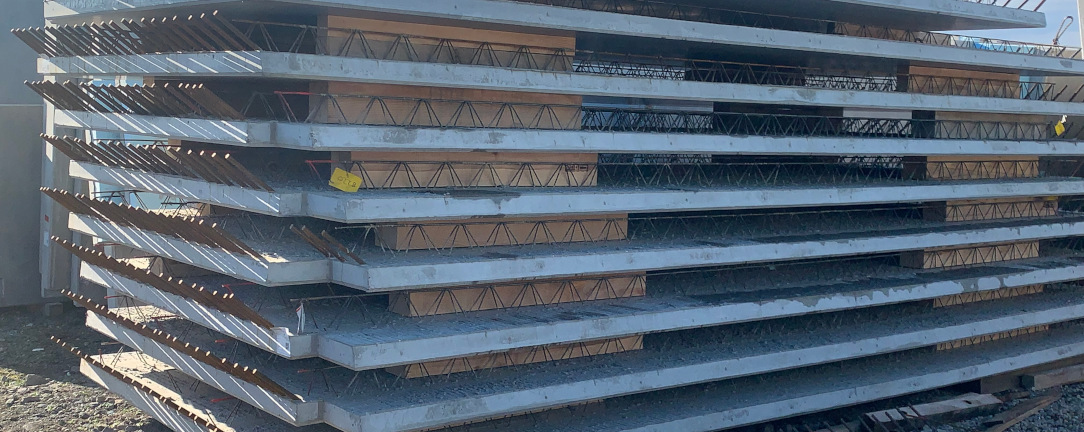
It provides a solution for fast feasible slab construction, a prestressed slab manufactured by our company.
The panels consist of 14 cm precast reinforced concrete slab and on-site reinforced wall concrete. The resulting slabs fully comply with both the static and fire safety conventional reinforced concrete slab structure.
Benefits of using a prestressed slab:
- faster, easier execution
- no support is required up to certain dimensions
- its lower surface is smooth and easy to prepare for painting
- individual building geometry can also be used
The panels consist of 14 cm precast reinforced concrete slab and on-site reinforced wall concrete. The resulting slabs fully comply with both the static and fire safety conventional reinforced concrete slab structure.
Benefits of using a prestressed slab:
- faster, easier execution
- no support is required up to certain dimensions
- its lower surface is smooth and easy to prepare for painting
- individual building geometry can also be used
Stairs
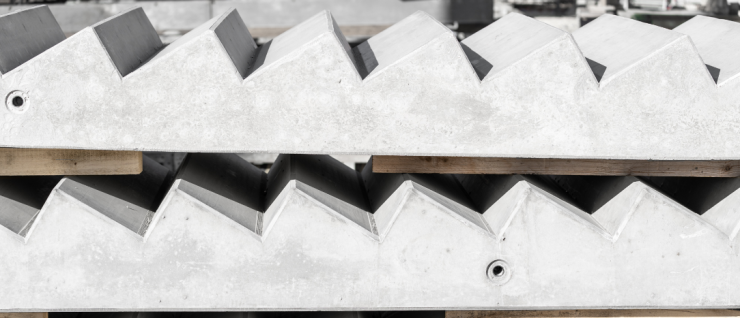
In order to speed up construction work, prefabricated stairs and rest areas provide an economically favorable, fast and accurate option.
- Labour-intensive on-site formwork can be replaced
- The batteries can be loaded immediately after placement
- Stairs can be made without rest or with lower and/or upper rest
- The stairs are made with all common up and entry size
- The steps can be made in faceted, rounded or cornered designs
- The upper surface of the staircase is made of apparent concrete quality, while the lower surface is plastered, prepared for painting and peeling
- The elements are delivered to the installation site "Just in time", which are placed by the construction company
Column
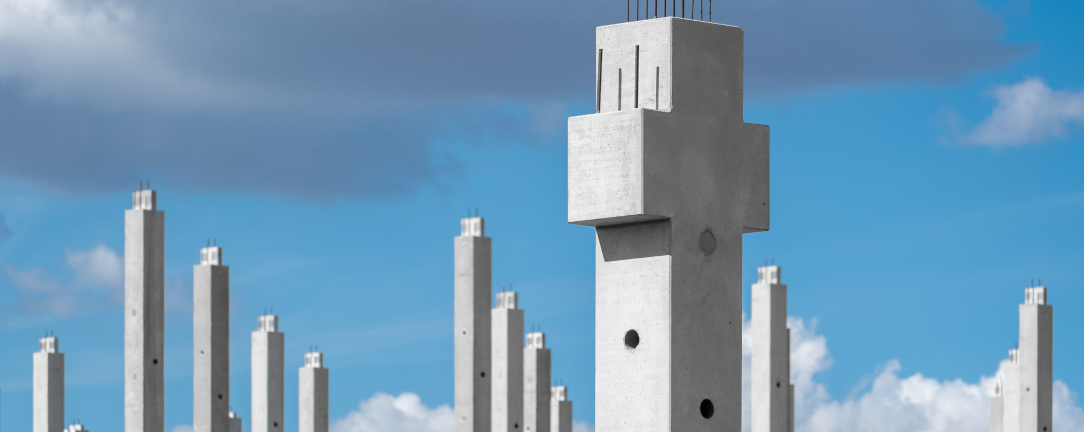
Industrial hall pillars can be made in length and cross-section according to static calculations.
Brackets can also be designed to receive connecting beams and crane tracks at desired places. The design of 4-sided brackets should be avoided for manufacturing reasons. The head design of the pillars can be chosen based on the type of beams. The products can be made in one or more tiered versions.
Our small pillars are set in visible concrete quality in our unique template park. The products can be made up to a height of 6 meters with rectangular, square circular and oval cross
sections. The pillars are usually attached to a monolithic slab. The load transfer between the pillar and the slab/floor must be dimensioned according to the spreading surfaces. The penetration test must also be performed according to the standard.
The above parameters determine the design of the pillar head and foot.
Brackets can also be designed to receive connecting beams and crane tracks at desired places. The design of 4-sided brackets should be avoided for manufacturing reasons. The head design of the pillars can be chosen based on the type of beams. The products can be made in one or more tiered versions.
Our small pillars are set in visible concrete quality in our unique template park. The products can be made up to a height of 6 meters with rectangular, square circular and oval cross
sections. The pillars are usually attached to a monolithic slab. The load transfer between the pillar and the slab/floor must be dimensioned according to the spreading surfaces. The penetration test must also be performed according to the standard.
The above parameters determine the design of the pillar head and foot.
Column with footing
In some cases, the pillar and foundation may be installed on site at the same time.
Our company also offers a solution for this case, with the production of footrest elements.
In this design, the pillar and foundation are fabricated and concreted together and delivered to the site.The dimensions of the pillars are fixed to a certain extent, but in order to receive connecting beams and crane tracks in the desired places, brackets can also be formed. The design of 4-sided brackets should be avoided for manufacturing reasons.
Our company also offers a solution for this case, with the production of footrest elements.
In this design, the pillar and foundation are fabricated and concreted together and delivered to the site.The dimensions of the pillars are fixed to a certain extent, but in order to receive connecting beams and crane tracks in the desired places, brackets can also be formed. The design of 4-sided brackets should be avoided for manufacturing reasons.
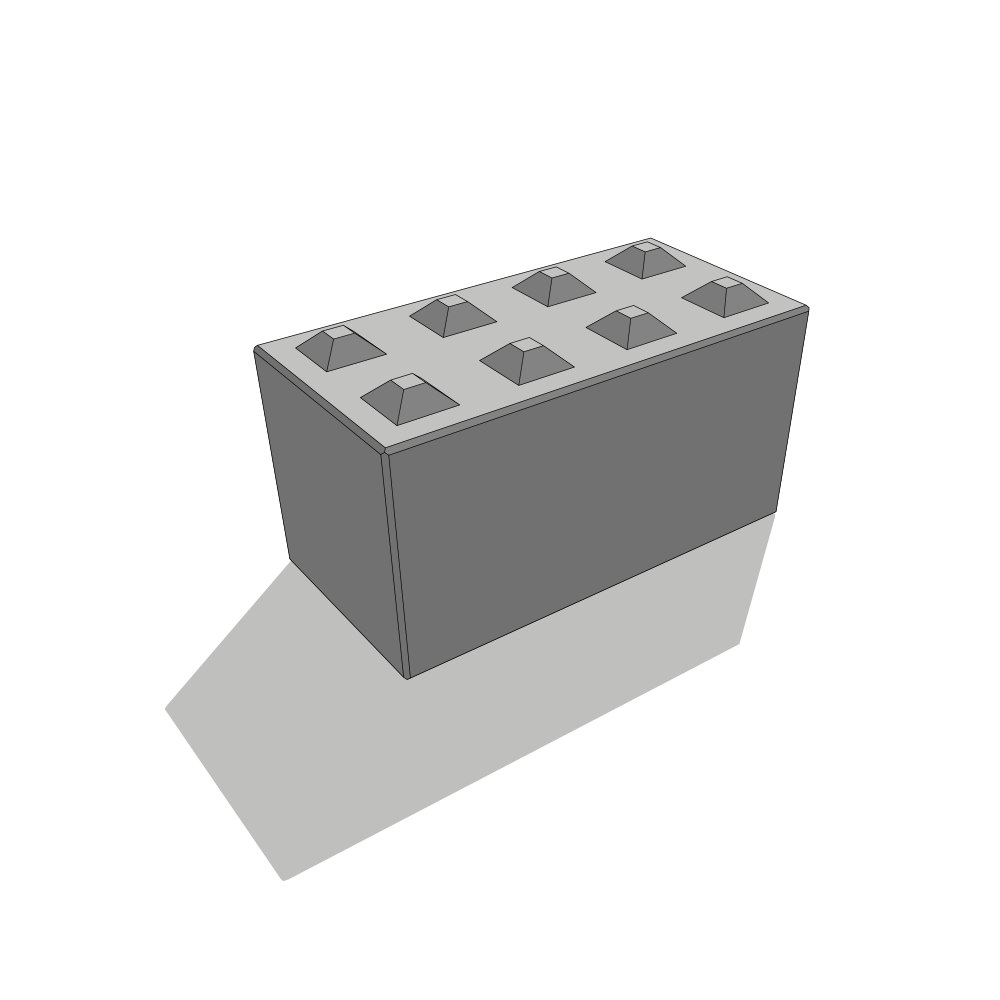
Concrete block
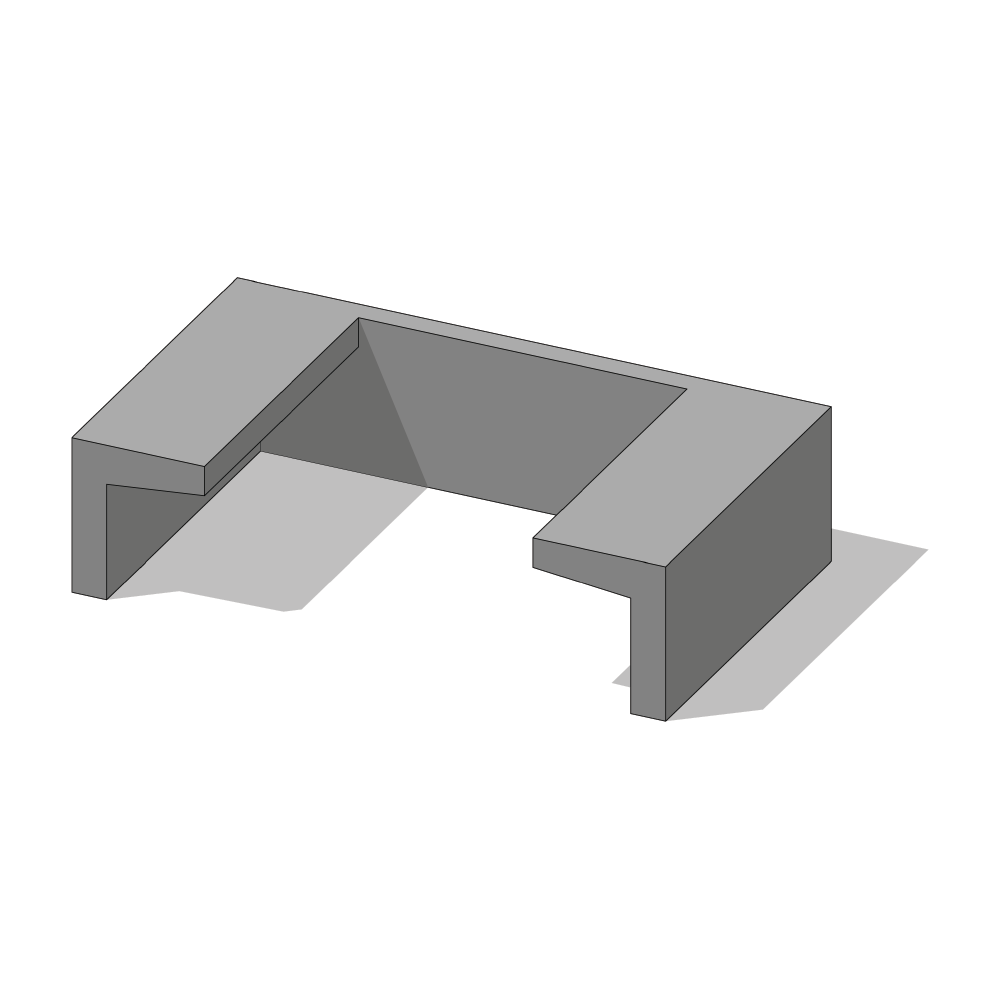
Docking station
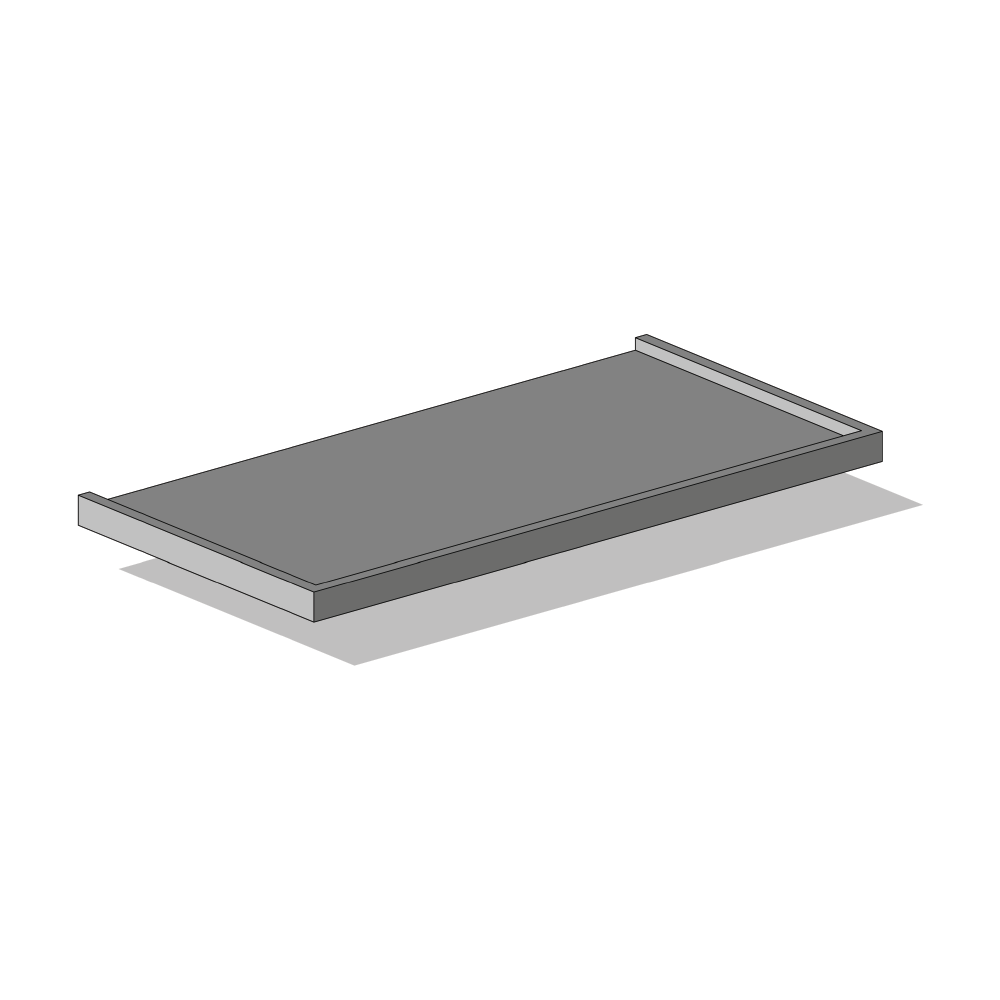
Balcony
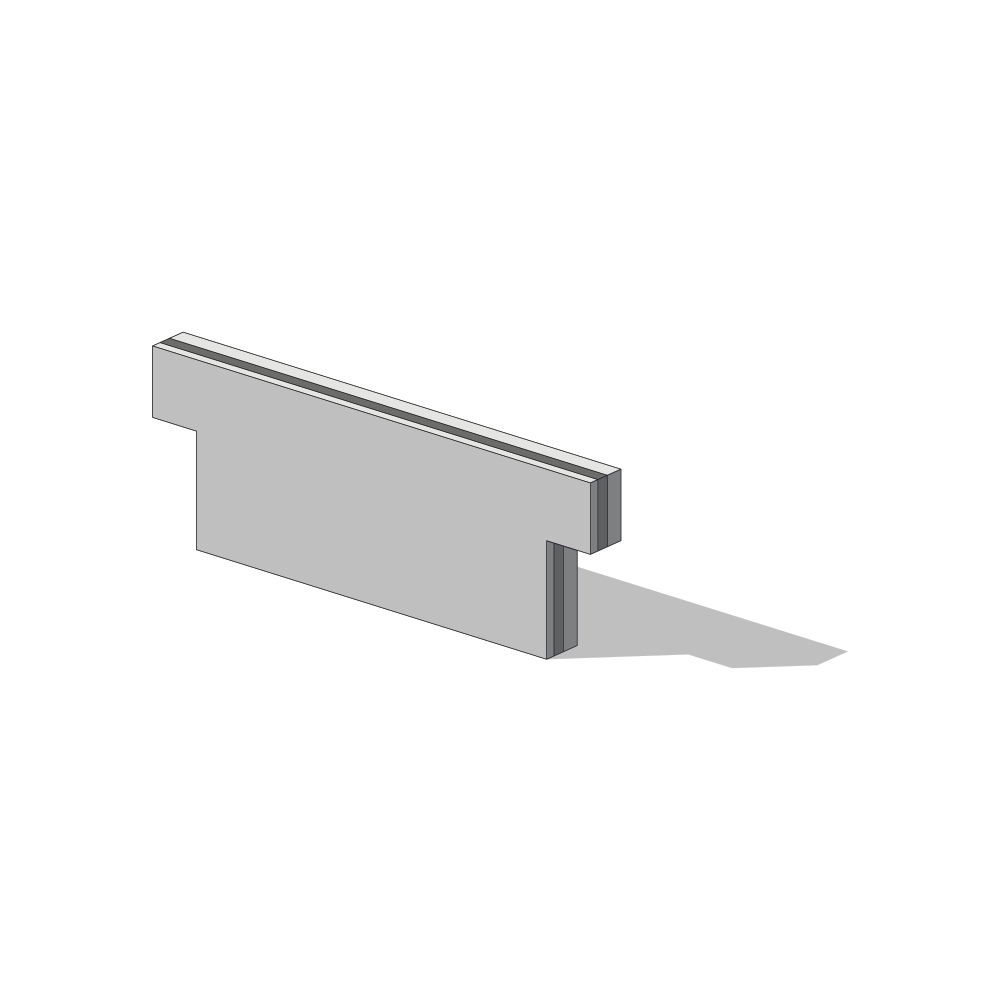
Wall panel
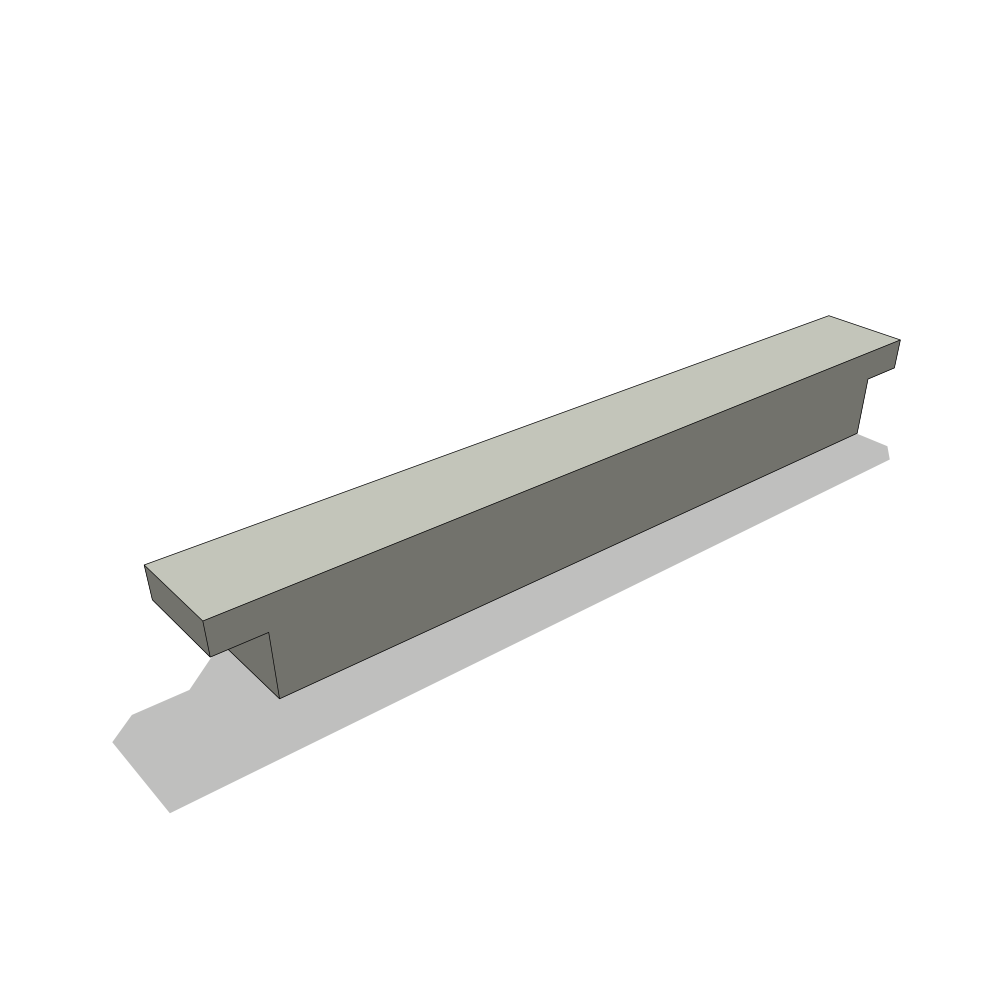
Beam
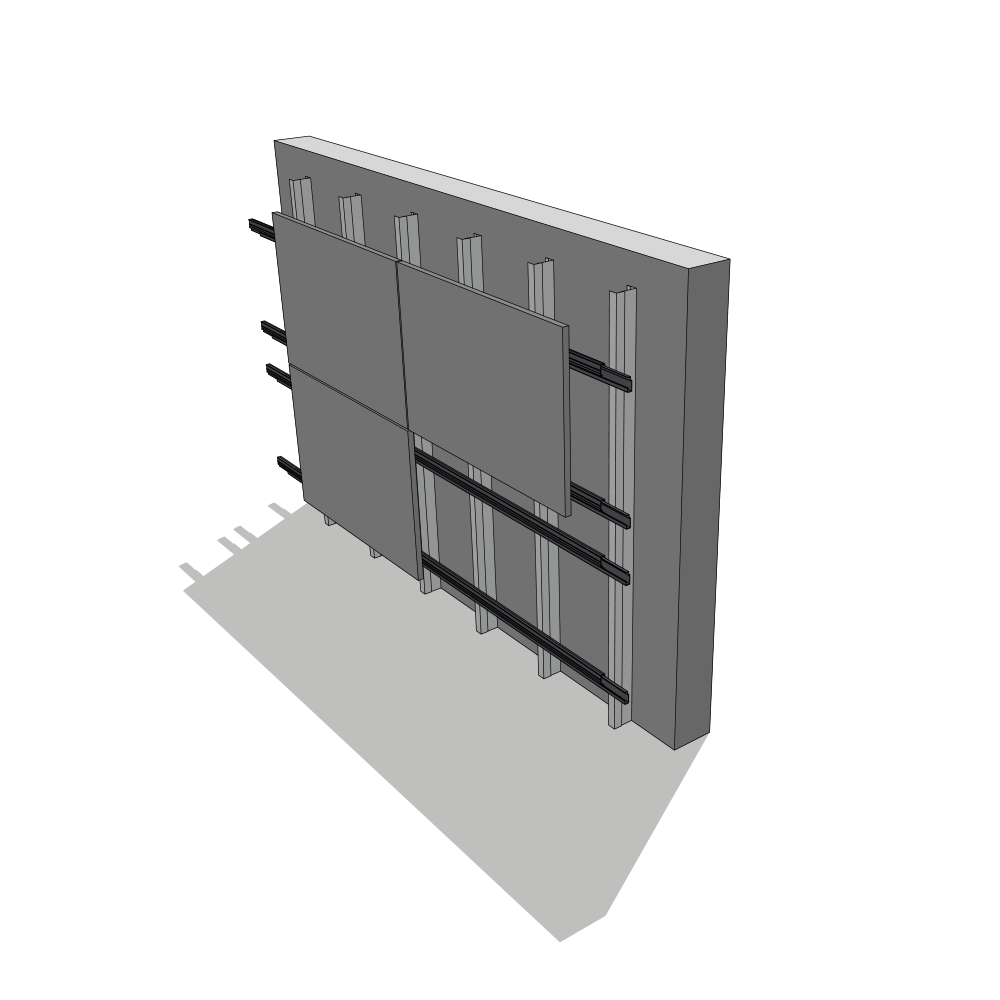
Facade panel
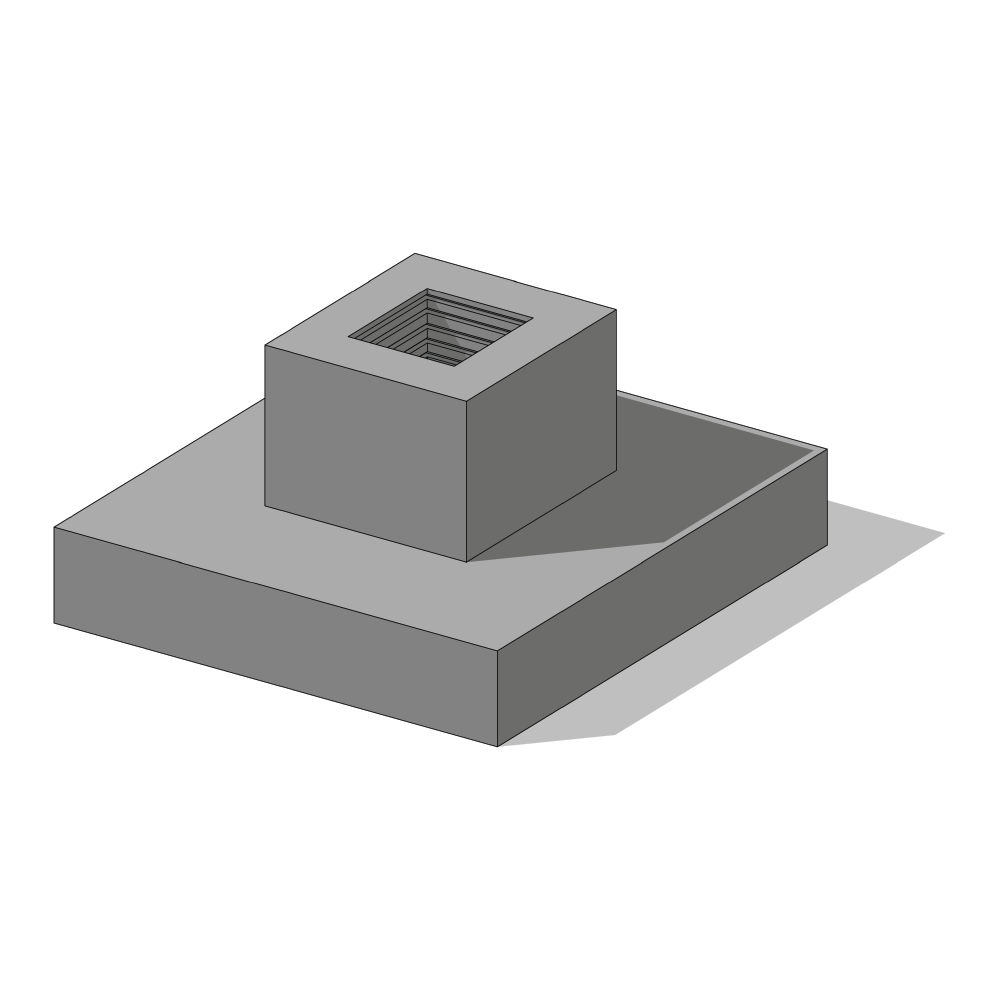
Cup
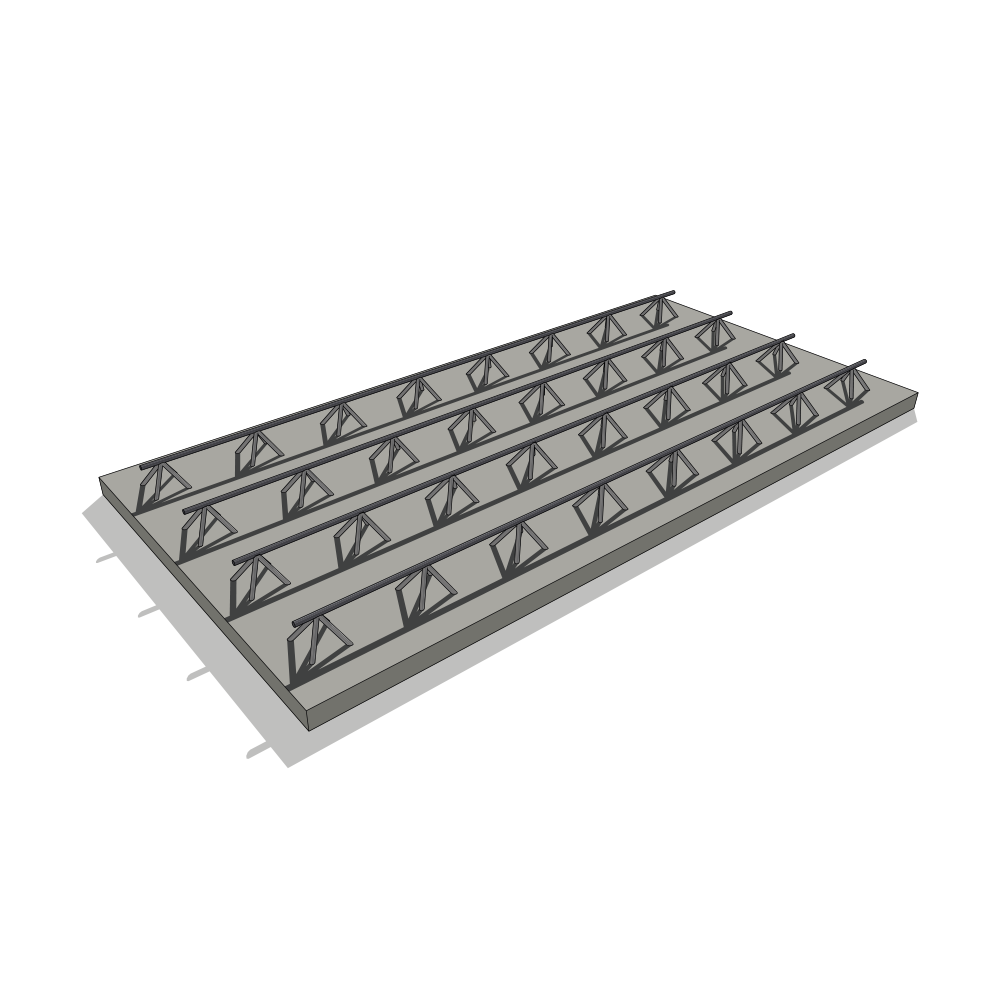
Prestressed slab
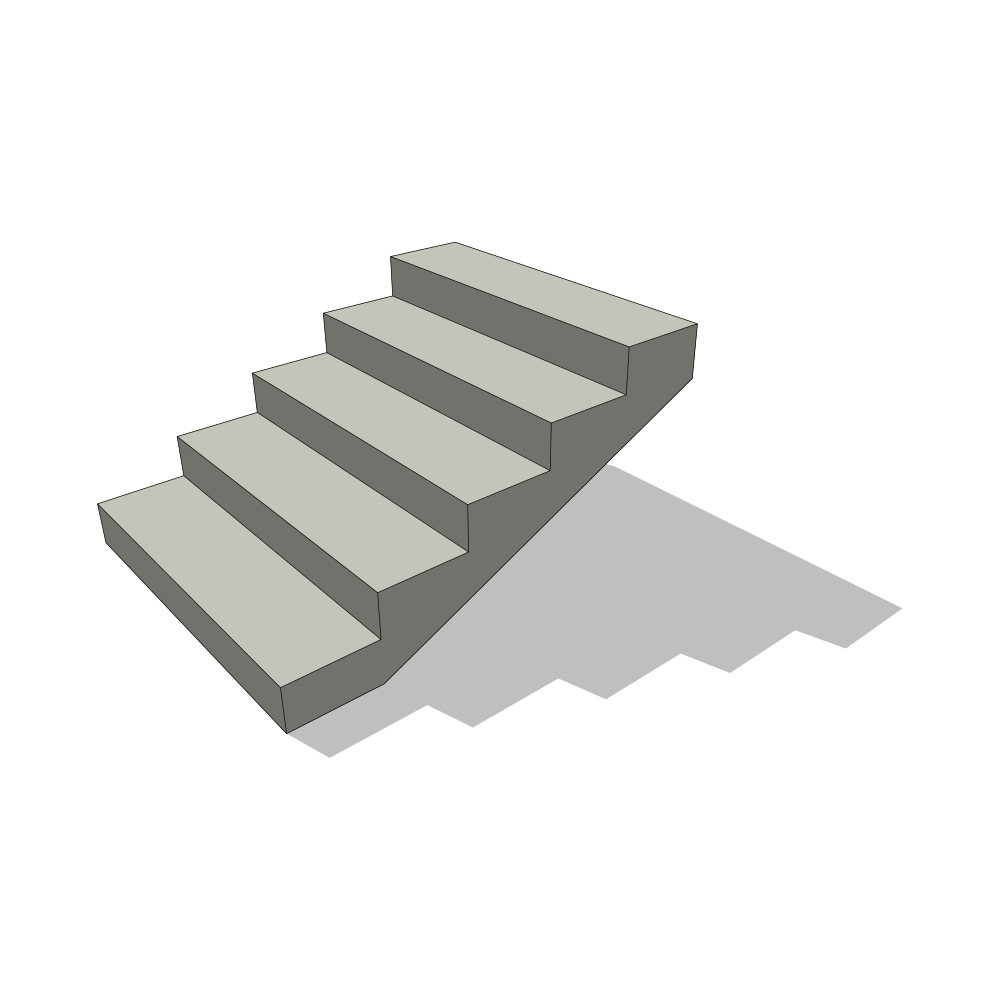
Stairs
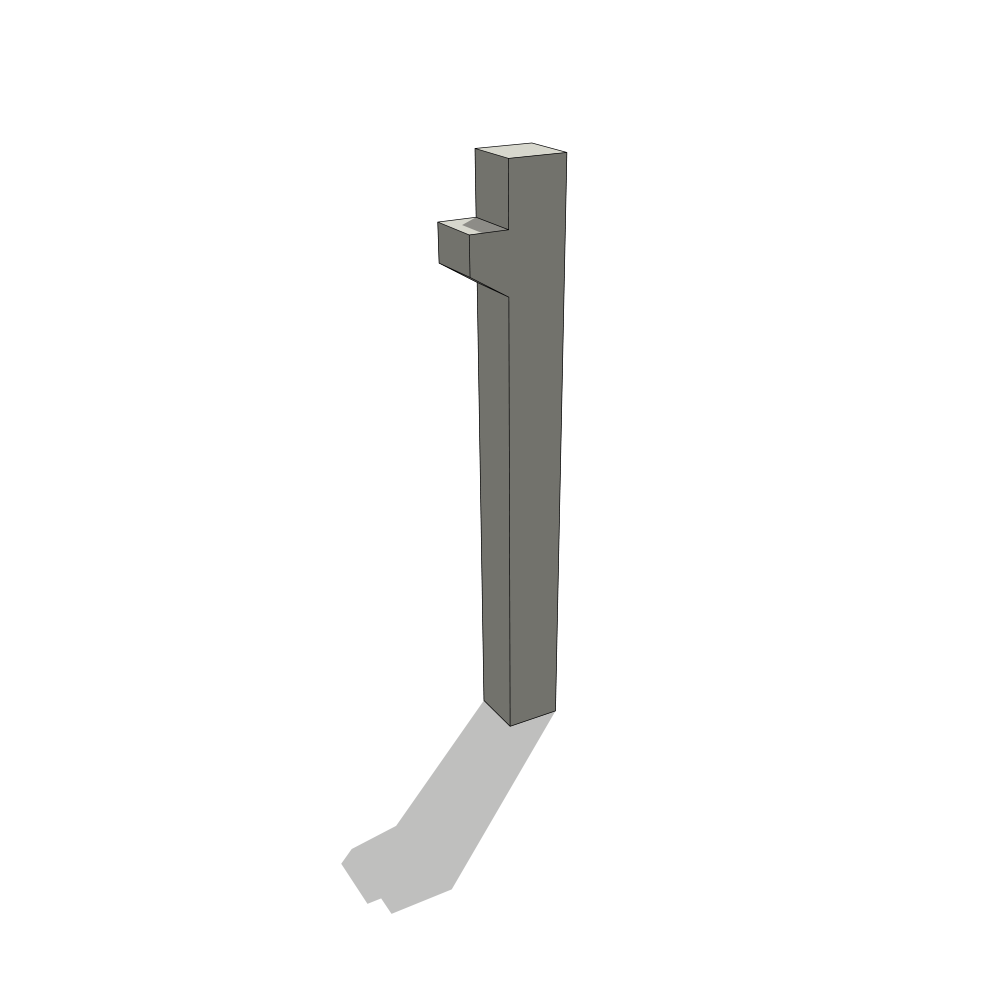
Column
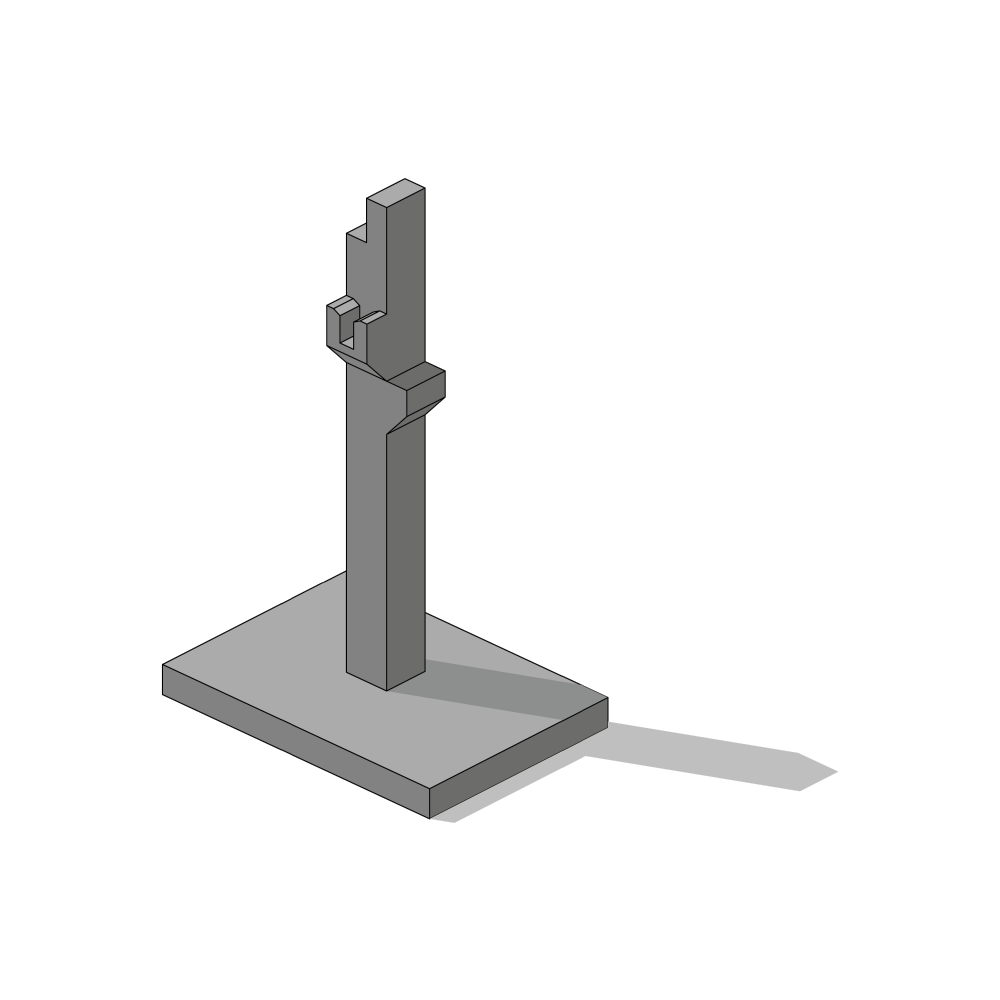